Rotary table for leak testing and component assembly for new Euro 7 Stellantis engines
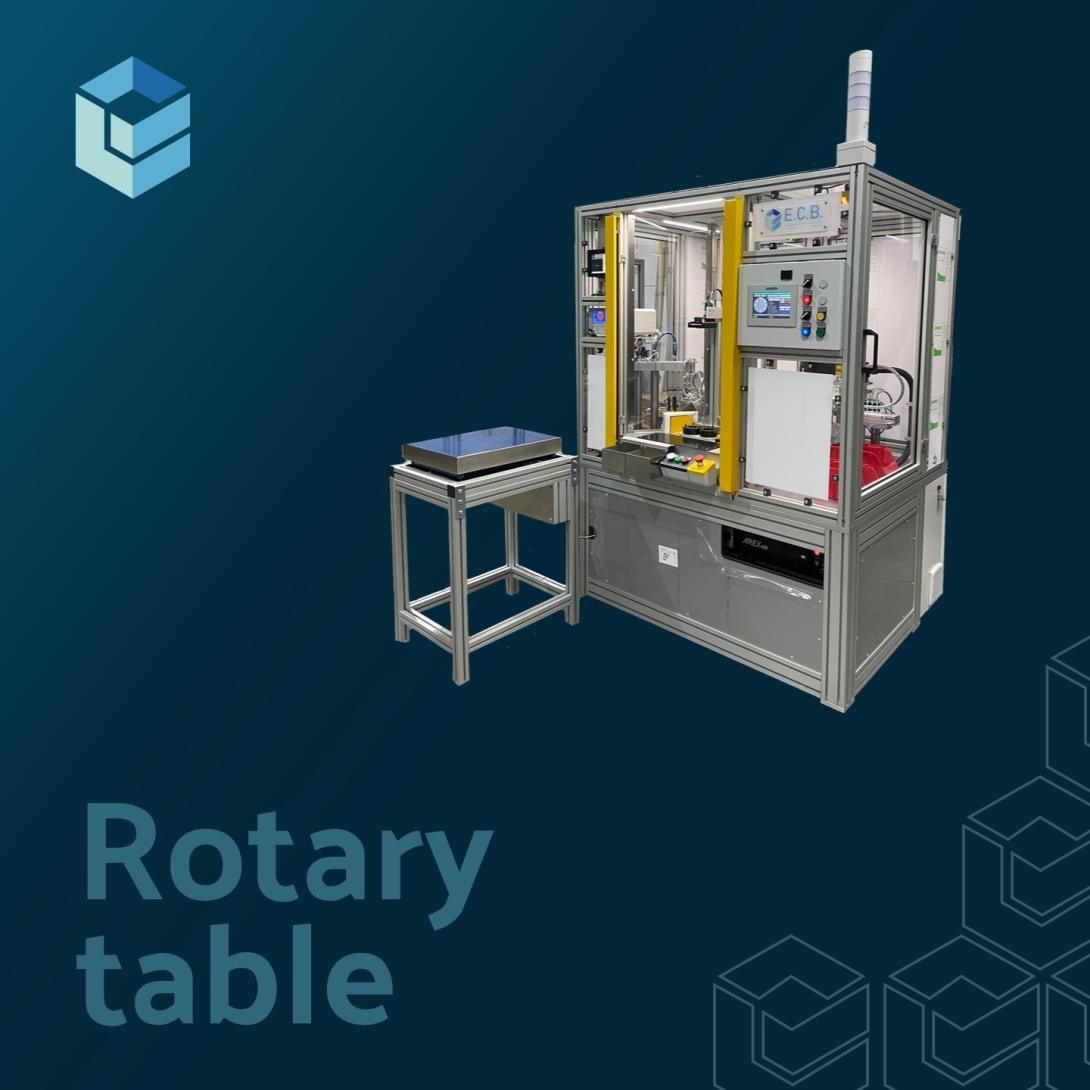
Despite what one might think, even seemingly simple components are very frequently subjected to quality testing before they can be delivered.
The increasingly restrictive requirements of customers, who demand defect rates now expressed in ppm (parts per million, i.e., very low percentages), no longer allow mass production and leave it to the customer to discard any non-conforming parts, but for just-in-time inventory management needs and to avoid any production slowdown, the latter expects to receive only conforming parts, subjected to the relevant quality checks.
An example of such parts could be the aluminum cover intended for the new Euro 7 engines for Stellantis commercial vehicles, for which we made a semi-automatic, manually loaded and unloaded rotary table capable of processing two different versions: one totally planar and blind, and another equipped with a mounting seat for an oil pressure transmitter.
The technical solution
The client required the following operations to be performed:
- Manual loading of bulk components;
- Leak test of the aluminum die cast to detect any die casting defects that would result in oil leakage;
- Assembly of the rubberized aluminum gasket, with automatic bending of the retaining tabs;
- Tightening of the first captive screw;
- Final verification of correct assembly;
- Laser marking of the Datamatrix traceability code;
- Rereading and grading of the marked Datamatrix code;
- Possible automatic unloading of scrap parts;
- Manual unloading and packing with automatic packing weighing for monitoring proper packing.
The required productivity and the type of operations to be performed led to the implementation of the rotary table architecture, specifically with 8 stations, to be able to run the various stages simultaneously and contain the cycle time while ensuring the required standards.
The operations were then divided over the 8 available stations:
- Station 10: Manual loading/unloading performed by the operator, who is responsible for "kitting," i.e., loading the 3 components onto the pallet, and unloading and packing the compliant parts. A vision sensor monitors the correct loading of components to validate table rotation and prevent damage caused by incorrect positioning on the pallet;
- Station 20: leak test, performed by an ECB TLD-1 leak meter that pressurizes the lid and monitors its pressure decay;
- Station 30: gasket assembly by overlapping the lid to the gasket and subsequent two-step automatic folding of the retaining fins;
- Station 40: captive screw tightening, by automatic screwdriver;
- Station 50: final optical inspection for evaluation of correct assembly and folding of the gasket fins;
- Station 60: laser marking of the Datamatrix identification and traceability code, with preliminary cleaning of the marking area by annealing for removal of surface oxides;
- Station 70: Datamatrix marked code re-reading, marking grading evaluation and possible automatic discharge of rejects into appropriate collection container;
- Station 80: free station, available for possible further final operations on good parts only.
ECB unique partner for providing automation and testing systems
Strengthened by the experience accumulated in more than 30 years of applications in the field of industrial testing, we are able to offer our customers an all-round service:
- Preliminary analysis of customer specifications and definition of optimal technical solutions;
- Mechanical, electrical, pneumatic and electronic design, all developed in-house. This allows us to always have an overview of the system being supplied;
- Optimized automation solutions for every need, from manual test bench to rotary tables and robotic islands;
- Customization of control software: every customer has different needs, implementing dedicated functionality is our standard.
Would you like to receive more information about rotary table or other testing automations? Contact us.