Leak testing challenges seem impossible? Not always, with the right expertise
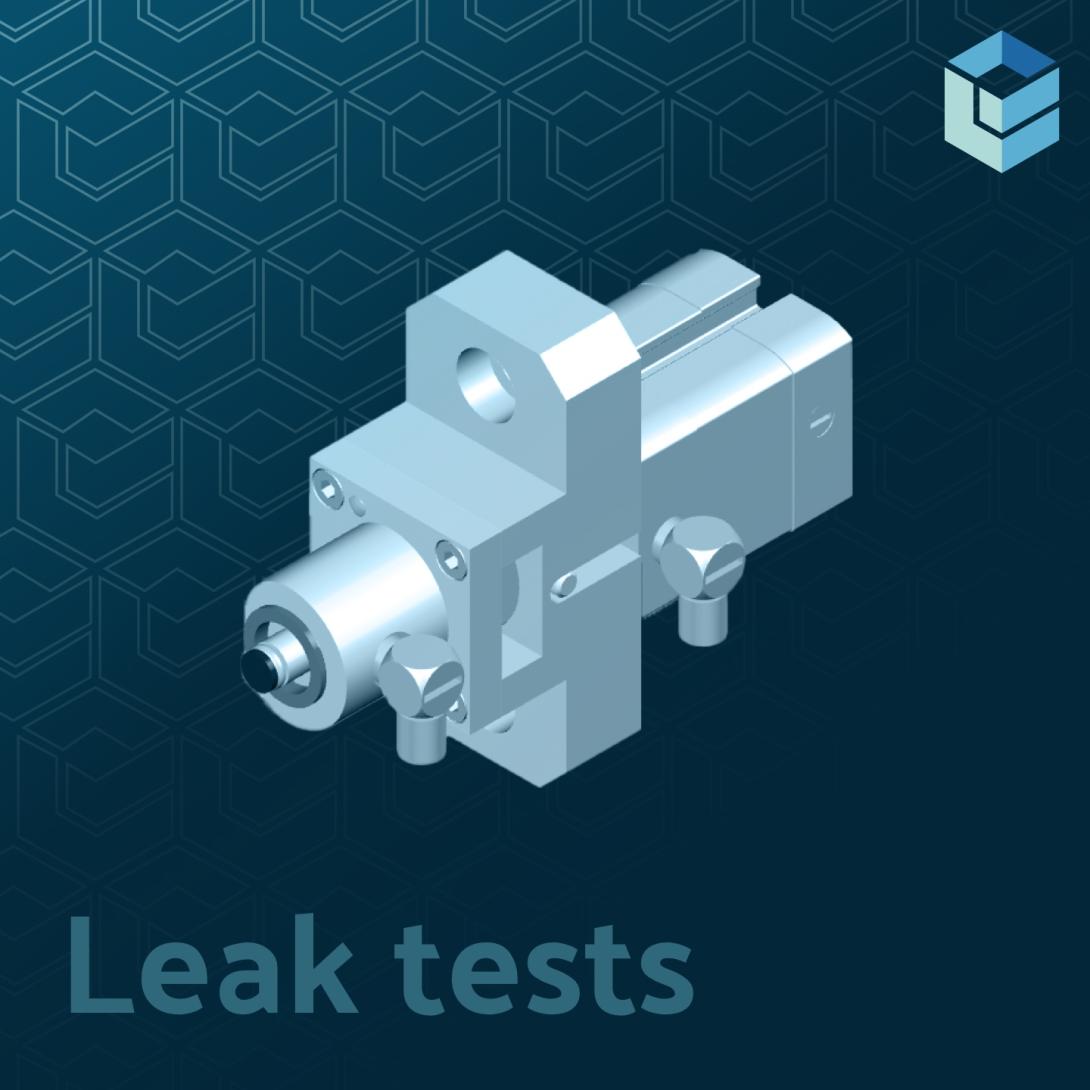
The leak testing of a product typically involves pressurizing or depressurizing its internal volume, which, in the event of a sealing defect, would allow communication with the external environment, leading to a progressive decline in the initially achieved pressure or vacuum level after pressurization or evacuation.
This method requires the leak testing system to have an "access door" to the internal volume for pressurization or evacuation, and then to monitor the relative pressure in real-time against barometric pressure. There are instances where these channels are specifically designed during the product development phase to facilitate leak testing in production, which are then sealed off by welding, resin sealing, or the installation of ventilation caps/barometric balance membranes.
But what about when the product to be tested is completely sealed, lacking any conduit for communication between the external and internal environments? Consider, for example, a simple ping-pong ball or a float. And what if the area to be pressurized is limited to just the walls of the conduit because sealing gaskets are in operation there, but the product by nature is not sealed?
Many industrial products fall into such categories, to name just a few: ventilation caps, barometric pressure sensors, retroreflectors, submersible sensors, washable relays, or completely sealed control units. These applications might mistakenly be considered "impossible”, unsuitable for leak testing, but in reality, many of them can be addressed with proper measures that can be summarized into a mix of technical solutions and appropriate selection of components used.
For instance, for testing a ventilation cap like the one shown at the top left in the image, the challenge is to plug the portion of the conduit between the Goretex® membrane and the external sealing o-ring to verify that the o-ring seals as expected on the conical seat present in the mounting location. On a production line of brushless motors for Hyundai, we addressed this issue by designing and creating a miniaturized plugging unit with double sealing, both frontal and radial internal expansion of 6 mm diameter, as shown in the figure.
In the case of completely sealed components without access to pressurize or evacuate the internal volume, the possibilities for leak testing might seem nonexistent, yet often they are not.
Referring back to the products depicted in the first image, some of the cases where this strategy can be applied include, for example, the testing of retroreflectors and sealed or submersible sensors. If it's not possible to measure the pressure variation inside the object relative to the external barometric pressure, in many cases, it's feasible to measure the pressure change that a potential leak from the product causes in a pressurized containment chamber or one in which a vacuum has been created.
This method can be highly effective and also provide very high sensitivity if the geometry of the part being tested allows accurately replicating the external surfaces, but it requires certain precautions with the measurement circuit and test system settings to differentiate special situations, such as the presence of macroscopic sealing defects.
ECB: Consulting for Optimal Design and Supply of Turnkey Optimized Tools
With over 30 years of field experience and thousands of applications to our credit, we are well-positioned to assist our clients in ensuring the adoption of the most suitable technical solutions. We support our client partners from the co-design phase of the leak testing station, and can also supply the station on a subcontracting basis with a "turnkey" formula, ready for line-side installation.
Would you like to receive more information or a consultation for a leak testing application? Contact us.